DirectPowder™ Patented Process

High Yield
>95% conversion rate to desired powder size distribution and can be used directly in downstream manufacturing processes, eliminating waste from typical sieving and classification processes.
Tailorable PSD & Morphology
Enables particle morphology to be tailored for the user’s requirements–the process produces particle shapes from thin flakes and fibers to equiaxed, semi-spherical powders used in most additive manufacturing processes.
Microstructure Control
Room-temperature, solid-state process that maintains same microstructure / mechanical properties of the bar stock while eliminating inert gas entrapment or evaporation of high vapor pressure elements.
Batch-To-Batch Consistency
Automated control of powder production through the combination of standardized material feedstock, precision tooling, and software control, resulting in high-quality, consistent powder feedstock every time.
Energy Reduction
Does not require extreme temperature, inert gas, or high vacuum environments, enabling environmental sustainability with 90% reduction in CO2 emissions compared to atomization.
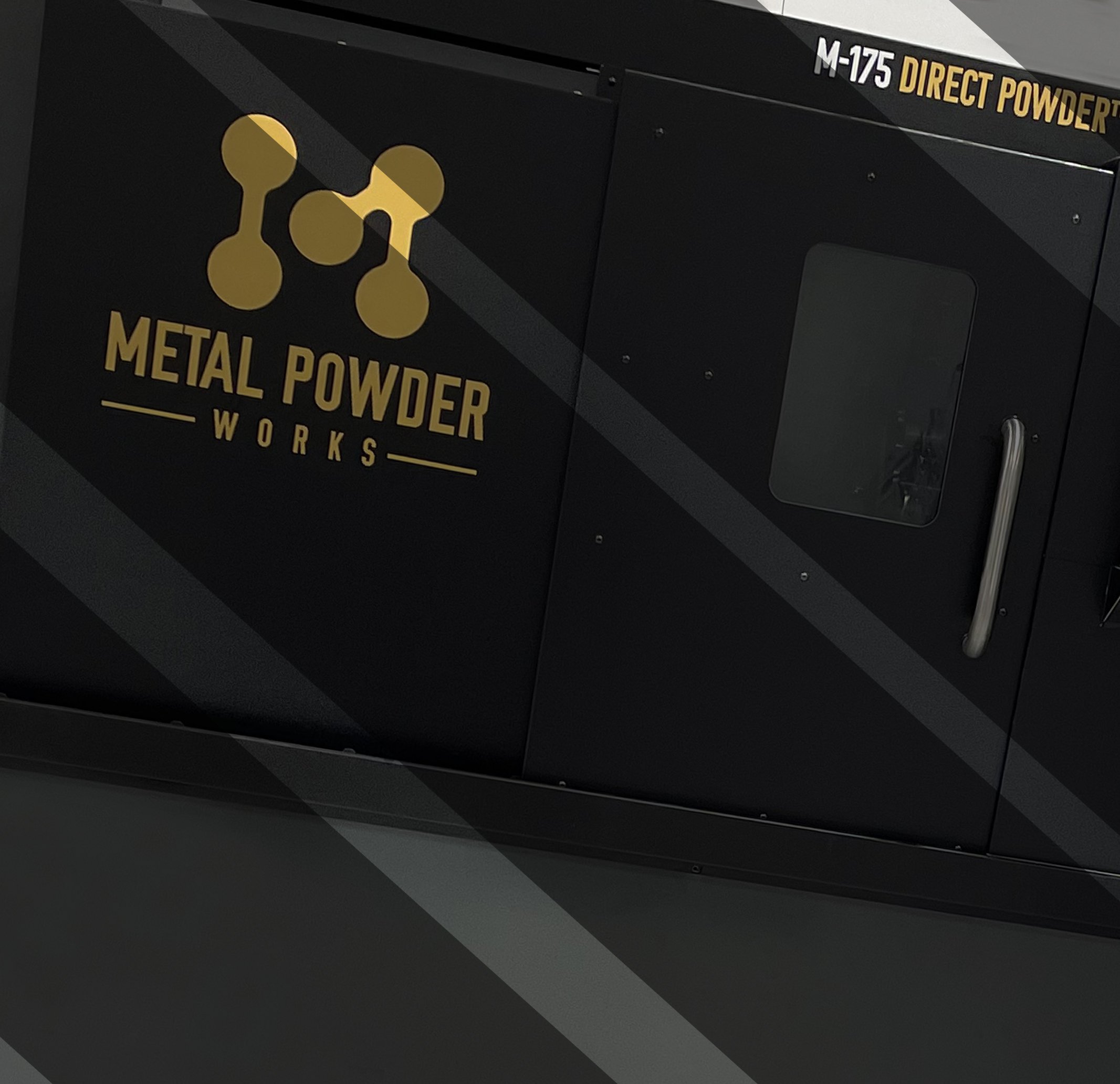
DirectPowder™ | Atomizing |
---|---|
>95% yield of desired powder size. Designed to make the desired PSD. | 20-50% yield of desired powder size. Sieving required to make desired PSD. |
Shape and size control from flakes to fibers and 0.7-0.8 sphericity. | No morphology control, produces 0.7-0.9 sphericity. |
Room-temperature, solid-state process that maintains the same microstructure and mechanical properties of the bar stock. | Requires melting and rapid solidification which can cause alloy segregation, unwanted phases, and elemental vaporization. |
100% fully dense particles. | May contain trapped gas porosity. |
No satellites with flowability. | Contains satellites that stick to particles and inhibit flow. |
Low-energy process with up to 90% reduction in CO2 emissions compared to atomization. | Energy-intensive process due to melting and inert gas usage. |
Wider range of processable alloys with bar stock. | Limited material selection based on feedstock availability and chemistry requirements. |
Batch-to-batch consistency with precise control over process dynamics. | Known consistency issues from batch to batch. |